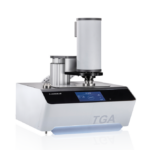
آنالیز حرارتی در صنعت فولاد
آوریل 7, 2025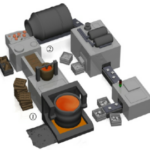
پارامترهاي مهم در فرآيند ريختهگري و شكل دهي فولاد
آوریل 12, 2025یکی از مجموعه آزمایشهایی که نقشی مهم در کنترل کیفیت، بهینهسازی تولید و افزایش بهرهوری در صنعت فولاد دارند با نام آزمایشهای فرآیندی شناخته می شوند به منظور حصول اطمینان از کیفیت محصول نهایی، لازم است تا این دستگاه ها بهطور مداوم پارامترهای مهم و مشخص شده را بررسی کنند. در ادامه، برخی از مهمترین دستگاههای آزمایش فرایندی و نحوه عملکرد آنها توضیح داده شده است.
1. آنالیزورهای گاز (Gas Analyzers)
به منظور اندازهگیری ترکیب گازهای خروجی از کورههای قوس الکتریکی، کورههای بلند و مبدلها برای کنترل احتراق و بهینهسازی مصرف انرژی از این آنالیزورها استفاده میشود. نحوه عملکرد آنها به این صورت است که با استفاده از سنسورهای مادون قرمز، لیزری یا طیفسنجی، غلظت گازهایی مانند CO، CO₂، O₂، SO₂ و NOx اندازهگیری میشوند.
2. طیفسنجی نشری (OES – Optical Emission Spectroscopy)
تعیین ترکیب شیمیایی فولاد و آلیاژها در حین تولید به وسیله این دستگاه صورت میگیرد. نحوه عملکرد آنها به این صورت که جرقه الکتریکی یا پلاسما، نمونه را تحریک کرده و عناصر مختلف آن، طیفهای خاصی از نور را منتشر میکنند که توسط آشکارساز ثبت و تحلیل میشود.
3. دستگاه XRF (X-Ray Fluorescence)
به منظور بررسی ترکیب شیمیایی مواد خام مانند سنگآهن، قراضه و همچنین آلیاژهای مصرفی از این دستگاه استفاده میشود. نحوه عملکرد آن به این صورت است که با تابش اشعه ایکس به نمونه، اتمهای آن تحریک شده و پرتوهای ثانویهای منتشر میکنند که مشخص کننده عناصر موجود در نمونه مورد آزمایش است.
4. آنالایزرهای کربن و گوگرد (C/S Analyzer)
به منظور تعیین مقدار کربن و گوگرد در فولاد و چدن، که بر خواص مکانیکی آنها تأثیر زیادی دارد از این دست از آنالیزورها استفاده میشود. نحوه عملکرد آنها به این صورت است که نمونه در کوره احتراق سوزانده میشود و گازهای CO₂ و SO₂ تولیدشده، با استفاده از آشکارسازهای مادون قرمز اندازهگیری میشوند.
5. آزمایشگرهای هیدروژن در فولاد (Hydrogen Analyzer)
به منظور اندازهگیری میزان هیدروژن محلول در فولاد مذاب که ممکن است باعث ایجاد تخلخل و ترک در محصول نهایی شود از این آزمایشگر استفاده میشود. نحوه عملکرد آن به این صورت است که نمونه گرم شده و هیدروژن آزادشده توسط یک آشکارساز گرمایی یا الکتروشیمیایی اندازهگیری میشود.
6. سختیسنجها (Hardness Testers)
به منظور اندازهگیری سختی فولاد برای اطمینان از تطابق با استانداردهای مکانیکی از این آزمايشگر استفاده ميشود. نحوه عملکرد آن به این صورت است که با استفاده از روشهایی مانند راکول (Rockwell)، ویکرز (Vickers) یا برینل (Brinell)، میزان فرورفتگی یک جسم سخت روی سطح نمونه اندازهگیری میشود.
7. دستگاههای آزمون کشش (Tensile Testing Machine)
به منظور بررسی استحکام کششی فولاد و آلیاژها نیاز به انجام این آزمون است. نحوه عملکرد آن به این صورت است که نمونه تحت نیروی کششی مشخصی قرار میگیرد و پارامترهایی مانند استحکام تسلیم، استحکام نهایی و درصد تغییر طول اندازهگیری میشود.
8. دستگاههای آزمون ضربه (Charpy Impact Test)
به منظور ارزیابی چقرمگی یا مقاومت در برابر شکست فولاد در دماهای مختلف نیاز به انجام این آزمون است. نحوه عملکرد آن به این صورت است که یک آونگ سنگین با انرژی مشخص به نمونه برخورد کرده و میزان انرژی جذبشده در هنگام شکست نمونه با ابزارهای مناسب اندازهگیری میشود.
9. تحلیلگرهای بازرسی سطح (Surface Inspection Systems)
به منظور شناسایی عیوب سطحی مانند ترک، پوستهشدگی و ناهمواری در ورقها و شمشهای فولادی نیاز به ابزارهای سنجش مناسب است. نحوه عملکرد آن به این صورت است که با استفاده از روشهایی مانند پردازش تصویر، لیزر اسکنر یا آزمایش جریان گردابی (Eddy Current Testing) عیوب سطحی شناسایی میشوند.
10. دستگاههای اندازهگیری ضخامت (Thickness Gauges)
اندازهگیری ضخامت ورقهای فولادی در حین تولید نورد گرم و سرد جز موارد مهمی است که باید انجام شود. نحوه عملکرد آن به این صورت است که با استفاده از امواج اولتراسونیک، لیزر یا پرتوهای گاما، فاصله بین دو سطح نمونه محاسبه میشود.
این دستگاهها در کنار هم، کنترل کیفیت فرایندهای تولید فولاد را تضمین کرده و به بهبود خواص مکانیکی و شیمیایی محصولات فولادی کمک میکنند.
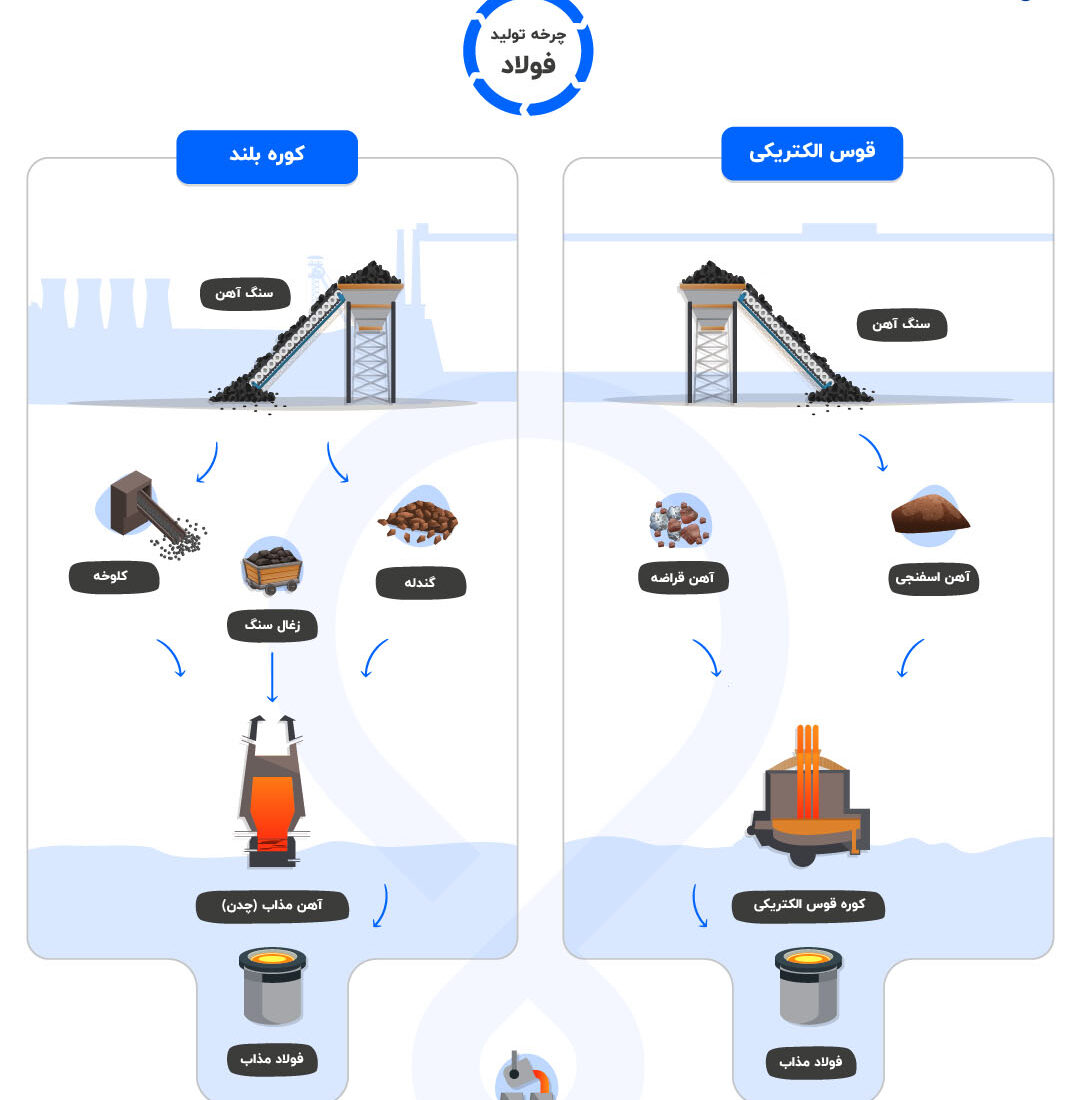
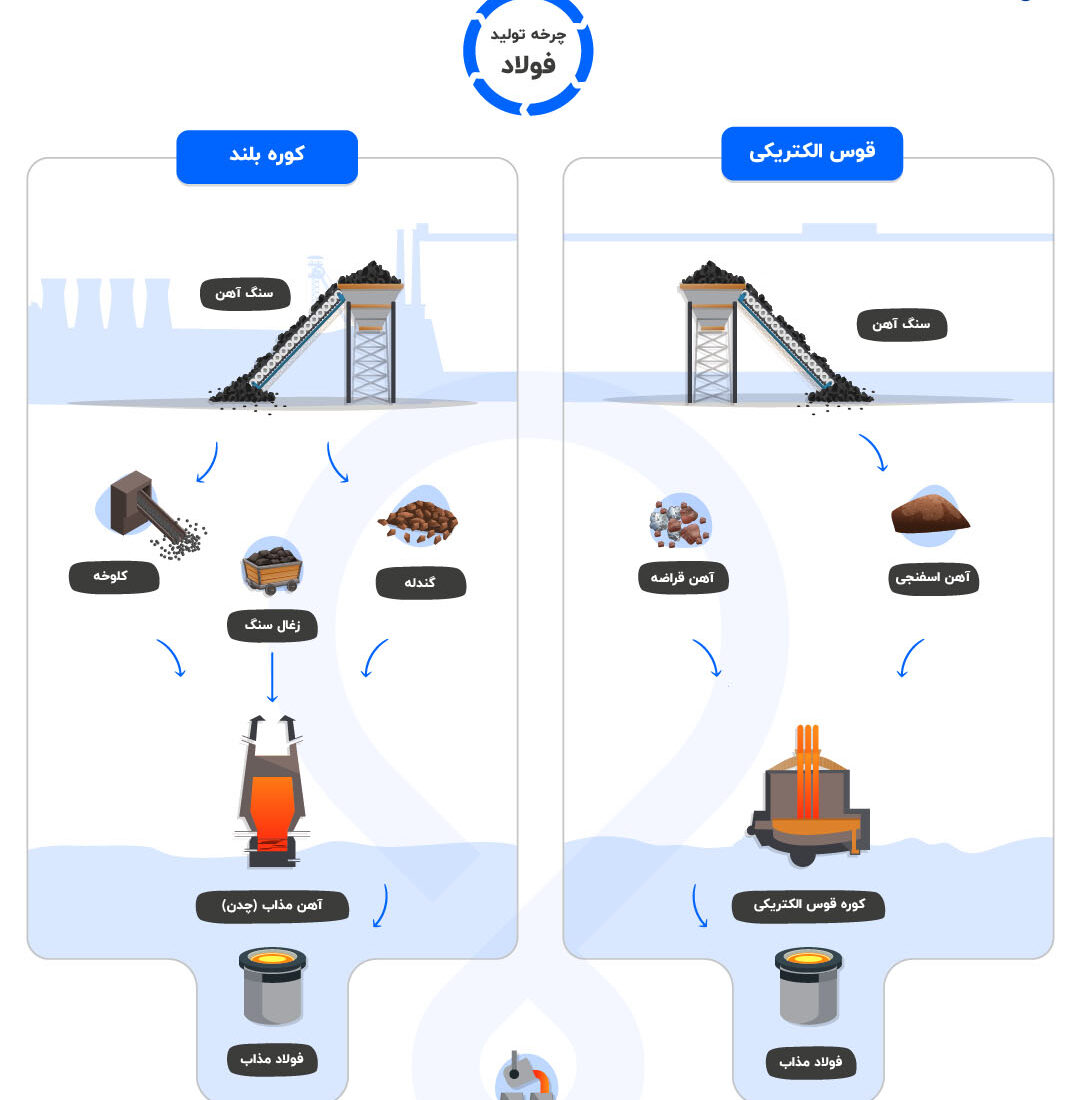